Printing a multi-material, SLA component with embedded NFC is difficult. Producing 300 a day with eight Ember printer, even more so. With all of the gloves, chemicals, post-curing, and cleaning, it's important to have a plan for a smooth production day.
To get a head start, I would get into the lab early each day to lay out production, repair, and research goals for the day. Although we were constantly producing tags for customers, our primary focus was improving our process through trial and error.
If you've ever worked with 3D printers, you know that repairs are a daily task, especially when you are running custom software for automating your machines. To reduce the amount of time we spent doing repairs, we began tracking temperatures of the resin vats during extensive printing, the effect of different torque values on the precision of the linear drives, and ideal cure values that produced solid parts but minimized the wear on our resin trays.
With Ember replacement trays always hard to come by, we tried very hard to get the most out of each tray.
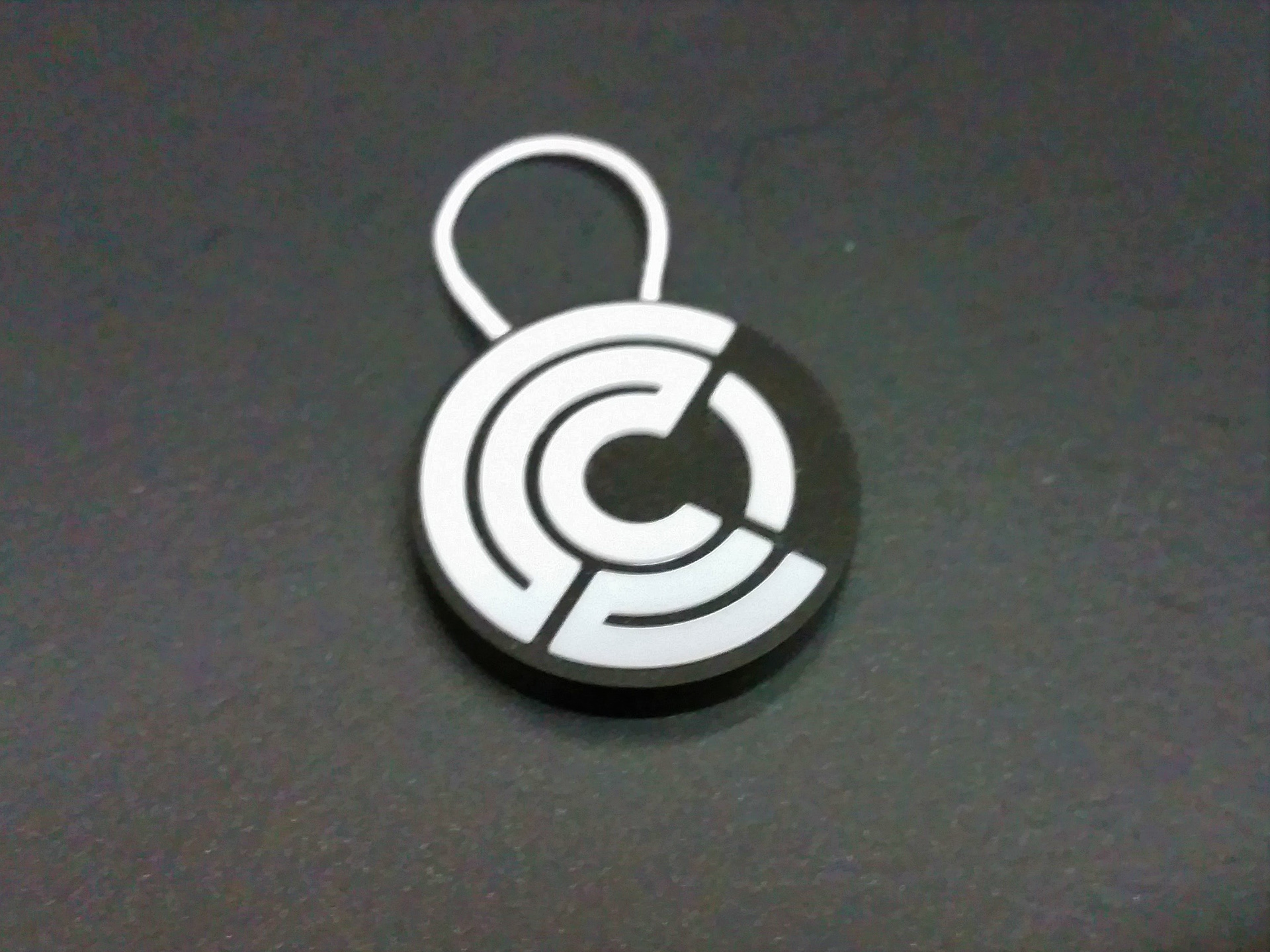
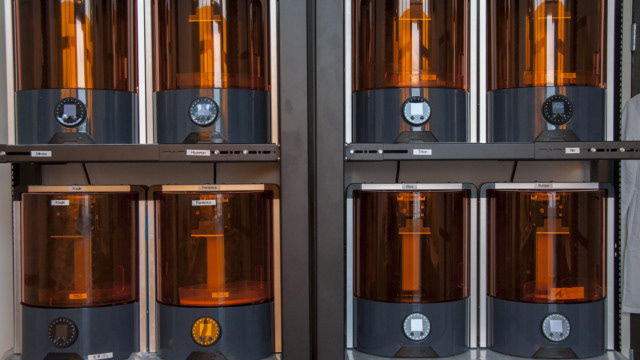
Located in a fantastically comfortable live/work office, our production equipment was set up in the "bedroom". Lucky for someone living in this space, but particularly unlucky for us, the room had vaulted ceilings and floor to ceiling windows across one entire wall. Cleaning was a constant necessity to prevent resin from curing and building up on our equipment.
To minimize the UV coming in, we applied UV resistant film to all of the windows we could reach. Effectively this turned the lab into an orange fishbowl. The fish bowl got especially hot on summer days when we'd need to crack the door open to prevent the machines from over-heating. . . who am I kidding, we were the ones overheating.
To reduce the amount of time we had to spend in this hot fishbowl, and to also make our production faster, I designed hand tools to work in conjunction with our custom fixtures and unique dual-material process. Not to mention some of them turned out looking pretty cool. The tool shown below has a flexible filament head to compress around the perimeter of a tag to aid in removal from a jig, without scoring the surface.
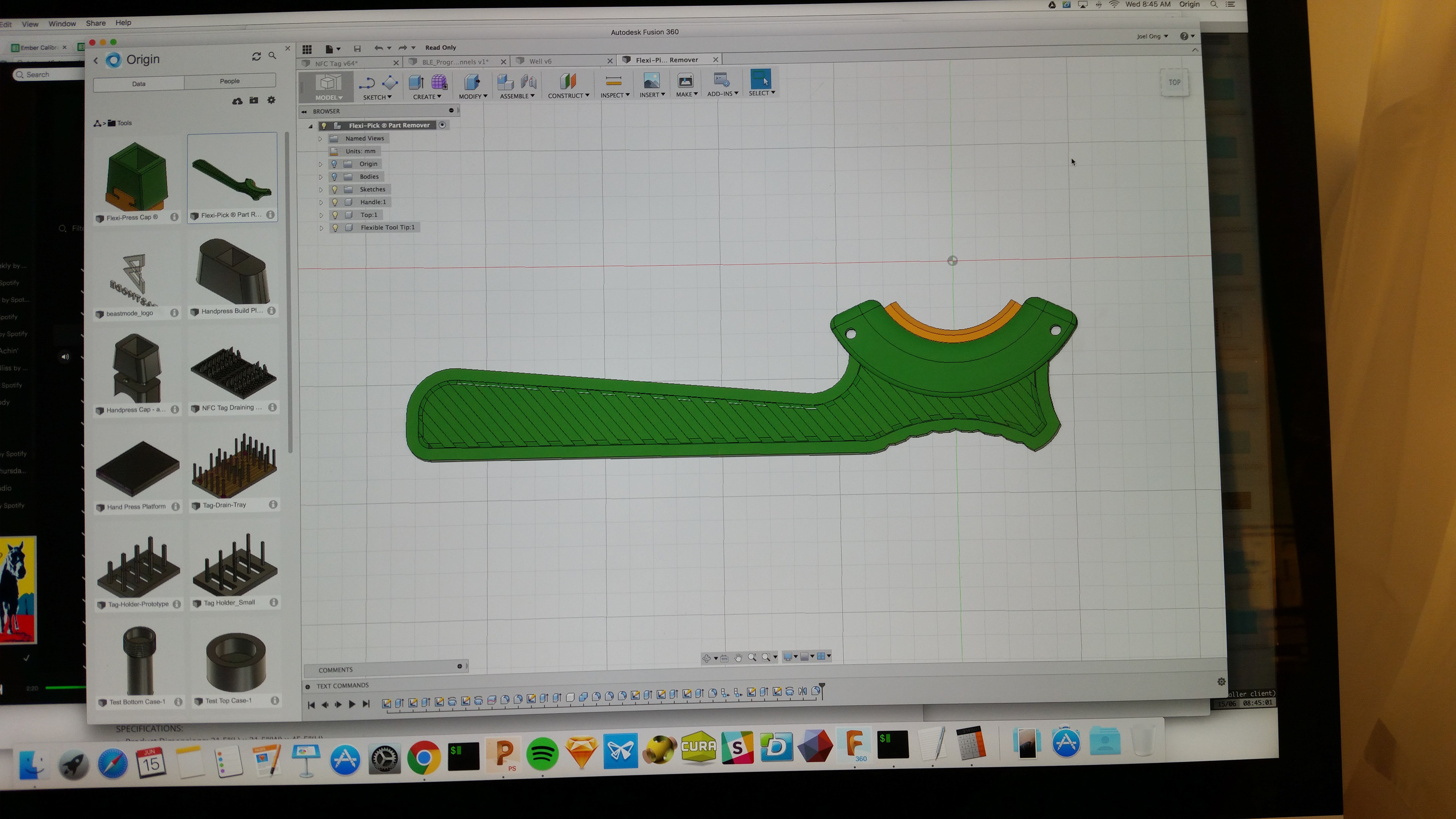
Part Removal Tool with Interchangeable Interface

Part Removal Tool in use
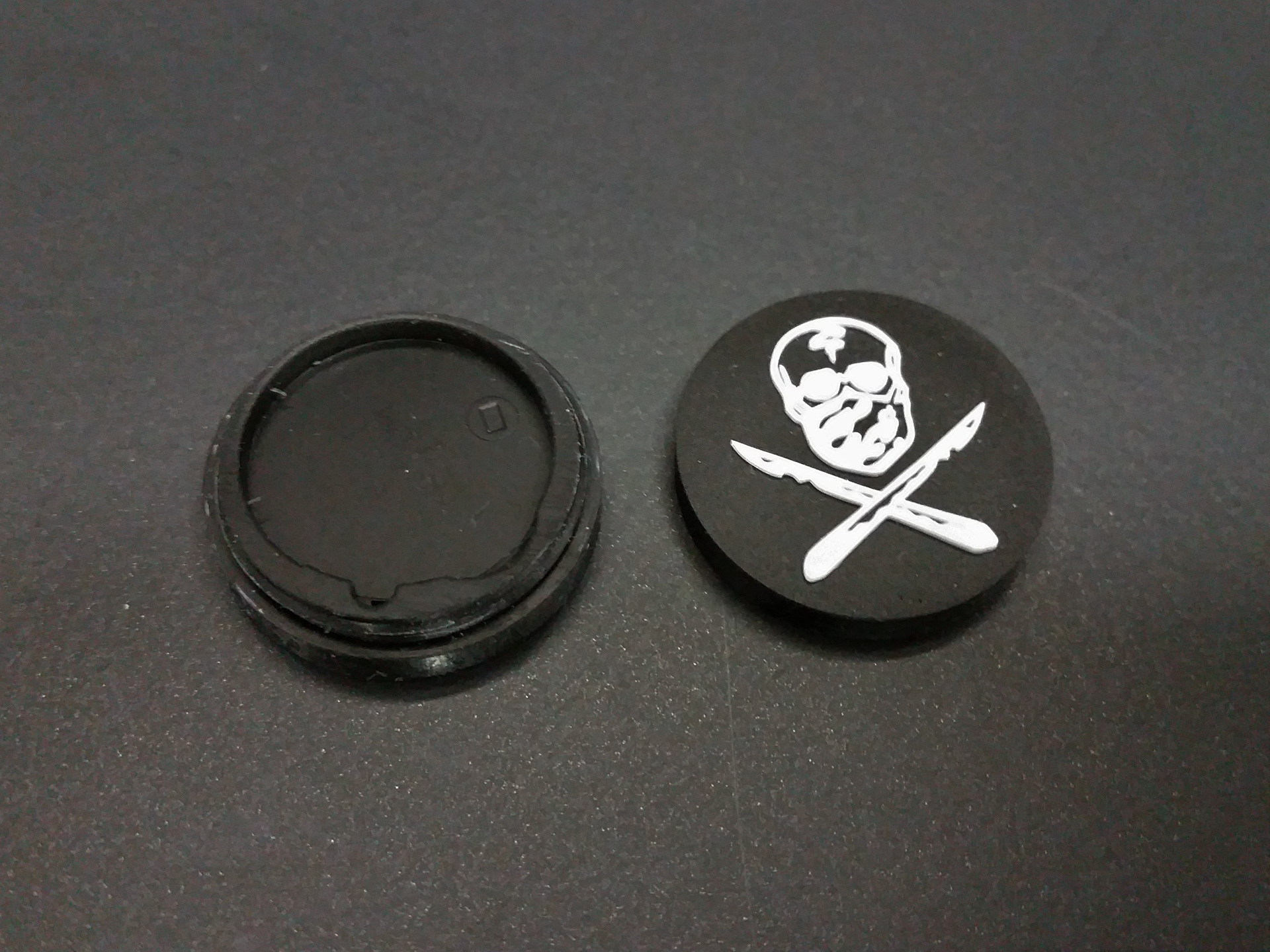