Background
A local company that produces medical compression socks, custom to a patient's unique foot and leg measurements, is in need of a custom iPad case to accommodate their 3D scanner.
The best way they found to get accurate foot measurements is with a 3DSystems scanner attached to an iPad. Running their own proprietary software, they can walk a small circle around the patient and have all of the information they need to produce the sock. The only issue they currently have with this process is that 3DSystems does not sell a case to accompany the scanner which attaches directly to the iPad.
My responsibility is to design two cases, one designed for production with additive manufacturing and the other to be mass-produced with injection molding.
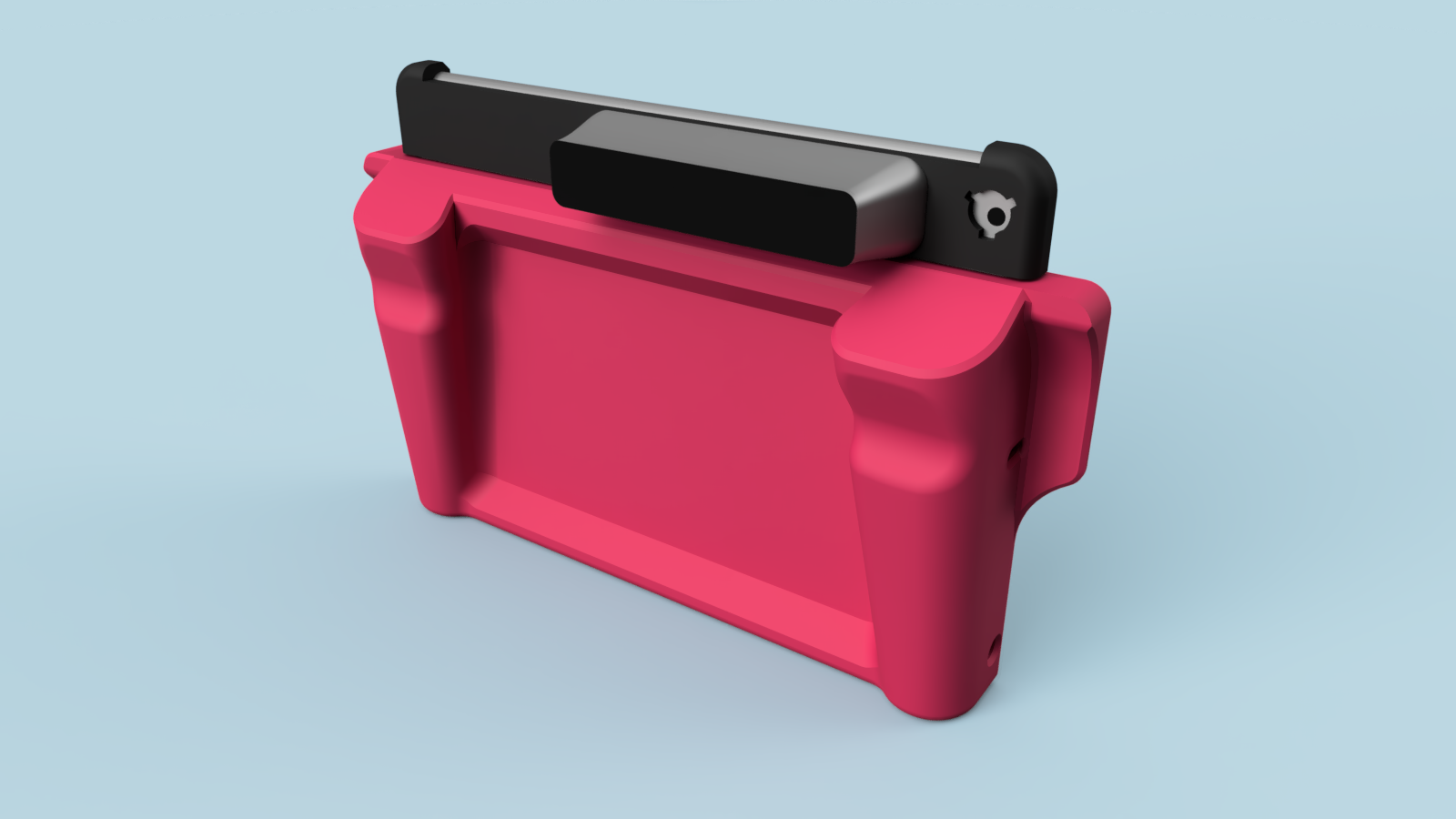
Design Considerations
- Ergonomic to hold while scanning a patient
- A place for thumbs to rest away from on-screen buttons
- Grips for fingers to wrap around, allowing one handed control if needed
- Clearance for scanner casing and optic's field of view
- Ability to protect scanner when iPad is set down
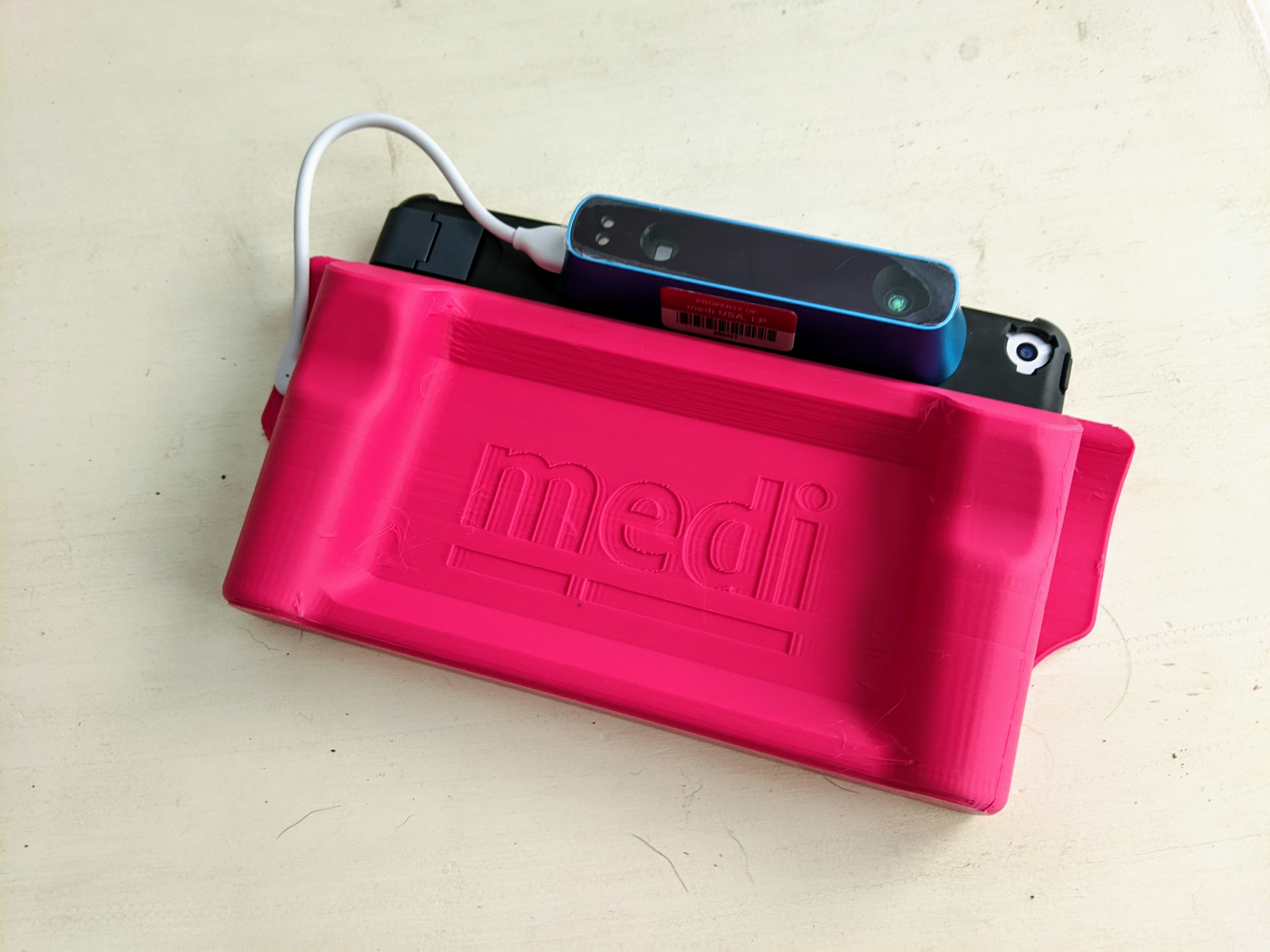
After successfully printing a case for the iPad version of their scanning assembly, a second version for their iPad Mini scanners was simple to create. Referring back to the variables table in my constrained Fusion 360 file, I altered the original dimensions of the iPad to automatically resize the case. This got me 80% of the way there. Going through the timeline, I was able to edit the existing design features to reflect the new, smaller form factor.
Currently, both versions of the scanner case have been approved. I am advising on print materials and finishing as well as helping to source a manufacturer for short-run additive production. A new version of the iPad is to be released soon by Apple, and with this next case design there will be modifications to allow for injection molding.